Der Vergaser
Eine bissige Definition
beschreibt den Vergaser als ein Gerät, das zu jeder Zeit genau das falsche Gemisch fabriziert.
Womit wir bei seiner Aufgabe sind: der Herstellung des Kraftstoff-Luft-Gemisches. Dieser Job ist
nicht so einfach, denn es müssen pro Kilo Benzin exakt 14,7 Kilo Luft dazugemixt werden. Weil 14,7
Kilo Luft schwer vorstellbar sind, haben wir beides in Liter umgerechnet: Zu 1,33 Liter Benzin
gehören 11369 Liter Luft. Dieses optimale Mischungsverhältnis wird als Lambda eins bezeichnet. Ist
mehr Benzin im Gemisch, sinkt Lambda unter eins; bei weniger Sprit steigt es darüber. Damit der
Motor überhaupt läuft, sollte Lambda zwischen 0,6 und 1,6 liegen. Aber: Der Katalysator
funktioniert am besten bei Lambda eins. Und den Wert zu treffen, bereitet mit einem Vergaser einige
Schwierigkeiten - weshalb er ab Mitte der Achtziger der präziseren Einspritzanlage Platz machte.
Deshalb beschränken wir uns auf die gebräuchlichste Form, den Einkammer-Fallstromvergaser. Der
besitzt nur eine Mischkammer, die alle Zylinder versorgen muß, und die Luft durchströmt ihn von
oben nach unten. Das ist problematisch, denn das Mischungsverhältnis darf nicht schwanken. Das
funktioniert am besten, wenn der Durchmesser der Mischkammer klein ist - weil dann die
Geschwindigkeit der Luft darin groß ist. Damit aber die Leistung des Motors stimmt, sollte der
Durchmesser groß sein. Deshalb wurden diverse Bauarten entwickelt. Etwa der Registervergaser, der
eine kleine Mischkammer hat für niedrige Last. Und eine große, die sich zuschaltet, wenn der Fahrer
mehr Gas gibt. Oder den Doppel-, Dreioder Vierfachvergaser, bei denen die entsprechende Anzahl
Mischkammern in einem Gehäuse sitzen und sich bestimmte Einrichtungen teilen. Etwa die
Schwimmerkammer: Diese speichert einen kleinen Kraftstoffvorrat, ein Schwimmer aus Kunststoff oder
Messing reguliert die Höhe des Spritpegels darin. Ist er zu niedrig, gibt er den Zufluß von der
Benzinpumpe frei, die den Kraftstoff aus dem Tank holt. Ist die Schwimmerkammer gefüllt, schließt
der Schwimmer den Zulauf. Durch das Mischrohr gelangt das Benzin dann in die Mischkammer, wird dort
von der durchrauschenden Luft mitgerissen. Am unteren Ende der Kammer befindet sich eine Klappe -
die Drosselklappe. Sie ist direkt mit dem Gaspedal verbunden, öffnet beim Gasgeben. Damit der Motor
aber nicht ausgeht, wenn die Klappe schließt, hat der Vergaser ein Leerlaufsystem. Das leitet einen
kleinen Gemischstrom um die geschlossene Klappe. Die meisten Vergaser haben auch oben eine Klappe -
die Starterklappe. Sie ist wichtig, um den kalten Motor zu starten. Denn dafür benötigt er mehr
Benzin. Die geschlossene Starterklappe verengt den Luftweg, erhöht so den Unterdruck - der Motor
saugt mehr Sprit durch den Vergaser und springt an. Nachteil: Der Verbrauch steigt in der
Kaltlaufphase enorm an. Auch hier hat die Einspritzanlage Vorteile: Ihre Düsen sitzen unmittelbar
vor den Einlaßventilen, das Benzin findet ohne Verluste zielsicher in den Brennraum.
Die Einspritzanlage
Bis weit in die
sechziger Jahre hinein hatte der Vergaser das Monopol bei der Gemischfabrikation. Dann stellten
steigende Anforderungen an Leistung und Schadstoffarmut seine Stellung immer stärker in Frage.
Dabei dachten die Konstrukteure schon lange über die Möglichkeit einer präziseren
Kraftstoff-Zuteilung nach. Erste Versuche begannen schon vor dem Ersten Weltkrieg. Ab Mitte der
zwanziger Jahre war die Benzineinspritzung Standard - allerdings nur bei Flugmotoren. Bei
Fahrzeugen dauerte es bis 1951. Dann ging im Gutbrod Superior die erste Einspritzung (von Bosch) in
Serie. Doch der Durchbruch gelang erst Mitte der Achtziger, als der frisch eingeführte Katalysator
nach einer besonders exakten Gemischzubereitung verlangte, um die Abgase bestmöglich zu reinigen.
Prinzipiell arbeiten alle Benzineinspritzungen nach dem gleichen Schema: Eine elektrische Pumpe
holt den Sprit aus dem Tank, setzt ihn unter Druck von vier bis fünf Bar. Ein anderes Gerät mißt,
wieviel Luft gerade in den Motor strömt, und meldet dies an ein Steuergerät. Das errechnet dann,
wieviel Benzin passend zur Luft eingespritzt werden muß, und öffnet die Einspritzventile.
Allerdings gibt es die unterschiedlichsten Lösungen für diese Aufgaben. Da wir hier nicht alle
beschreiben können, müssen wir uns auf die heute übliche, elektronisch gesteuerte Einspritzung
beschränken. Deren einzig ernsthaftes Problem ist die Erfassung der Luftmenge. Früher wurde dafür
eine Stauklappe im Ansaugweg benutzt, die mit einem Geber gekoppelt war. Aber: Diese Klappe
behindert den Luftstrom, kostet also Leistung. Deshalb finden seit Mitte der Achtziger zunehmend
sogenannte Hitzdraht- und später auch Heißfilm-Luftmassenmesser Verwendung. Dabei wird im Ansaugweg
entweder ein dünner Draht oder ein auf Keramik aufgedampfter Metallfilm elektrisch beheizt und auf
konstanter Temperatur gehalten. Die vorbeiströmende Luft kühlt ihn ab, so daß der Heizstrom erhöht
werden muß - woraus sich die Luftmasse errechnet. Positiver Nebeneffekt: Diese Messung
berücksichtigt auch Änderungen der Luftdichte auf Grund von Druck oder Temperatur - es wird die
tatsächliche Luftmasse erfaßt, beim Verfahren mit der Stauklappe dagegen nur die Luftmenge. Jetzt
muß die Elektronik nur noch die dazu passende Spritmenge ausrechnen und die Einspritzdüsen
entsprechend öffnen. Der Trick dabei: Die Einspritzmenge wird über die Öffnungsdauer der Düsen
geregelt. Und: Alle Düsen öffnen gleichzeitig, das Benzin wartet als Wolke vor dem Einlaßventil.
Bis es öffnet, der Kolben das Gemisch ansaugt und der Viertakt seinen Lauf nimmt.
Die Zündkerze
Nachdem Vergaser oder
Einspritzanlage ein Kraftstoff- Luft-Gemisch produziert haben, das vom Kolben zunächst angesaugt
und dann verdichtet wurde, muß es entzündet werden. Gar nicht so einfach, schließlich ist der
Brennraum ein Hochsicherheitstrakt aus Metall: Die Ventile sind geschlossen, der Kolben hat fast
seinen oberen Totpunkt erreicht - nichts geht mehr rein, nichts raus. Als das Auto fahren lernte,
behalfen sich die Tüftler mit einem glühenden Rohr im Zylinderkopf, an dem sich das Gemisch mehr
oder weniger zufällig entzündete. Doch bald erkannten die Kfz-Pioniere, wie wichtig die Zündung des
Gemischs zu einem exakten Zeitpunkt ist. Und so gebührt der Firma Bosch die Ehre, 1902 den
Hochspannungs- Magnetzünder und damit gleichzeitig die Zündkerze eingeführt zu haben. Der Trick:
Elektrische Energie wird zu einem Stromstoß gebündelt, der die Verbrennung in Gang setzt. Wie aus
zwölf Volt Batteriespannung 30 000 Volt Zündspannung werden, erfahren Sie allerdings erst nächste
Woche. Denn in dieser Folge geht es darum, den Zündfunken in den Brennraum zu lotsen. Keine leichte
Aufgabe, denn die Hochspannung würde lieber vorher ins Metall des Motors fließen, als zwischen den
Elektroden der Zündkerze als Funken überzuspringen. Deshalb ist eine Zündkerze ein
isolationstechnisches Kunstwerk, ein Verdienst des charakteristisch weißen Isolators. Bei Bosch
besteht er aus Aluminiumoxid, wird im Sinterverfahren hergestellt. Das bedeutet, daß aus dem
pulverförmigen Rohstoff unter hohem Druck und hoher Temperatur der Rohling gebacken wird. In seinem
Inneren befinden sich am unteren Ende dieMittelelektrode,vonderder Funken überspringt, oben der
Anschlußbolzen für den Kontakt zum Hochspannungskabel. Das Problem: Oben ist es kühl, im Brennraum
hingegen bis zu 3000 Grad heiß. Trotzdem muß die Verbindung der leitenden Teile absolut gasdicht
sein. Die Lösung: leitfähiges Spezialglas, das als Verbindung und als Dichtmittel wirkt. Bleibt nur
noch das Problem, den Isolator mit seinem leitenden Innenleben dauerhaft ans Gehäuse zu fesseln -
schließlich darf er bei Verbrennungsdrücken von bis zu 50 Bar nicht durch die Motorhaube schießen.
Die Fertigung des Gehäuses ist weniger spannend: Es besteht aus Stahl, erhält durch Kaltpressen
seine Form mit dem Sechskant für den Zündkerzenschlüssel. Die ein bis vier Masse-Elektroden aus
Nickel oder einer Nickellegierung werden angeschweißt, das Gewinde zum Einschrauben in den
Zylinderkopf wird gerollt. Zur Endmontage wird der Isolator ins Gehäuse gesteckt und der Kragen
oberhalb des Sechskants ebenfalls durch Kaltverformung geschlossen. Wichtig ist die Einschnürung
unterhalb des Sechskants: Sie wird zum Glühen gebracht, kurz angestaucht. Nach dem Abkühlen sitzt
der Isolator bombenfest, die Kerze ist fertig zum Einschrauben.
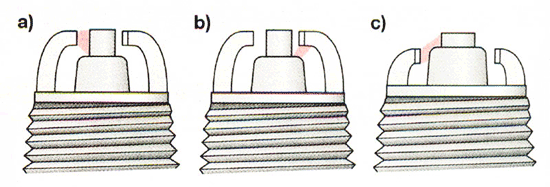
Die Zündspule
Damit das Kraftstoff- Luft-Gemisch zuverlässig verbrennt, muß an der Zündkerze ein Funke
überspringen - also ein Blitz. Doch anders als bei einem Gewitter, bei dem unterschiedlich
temperierte Luftschichten für elektrische Aufladung sorgen, wird beim Ottomotor dafür ein
spezielles Gerät benötigt - die Zündspule. Sie ist seit Einführung der Batteriezündung in den 30er
Jahren verantwortlich für zuverlässige Funkenbildung. Wenn wir ins Auto steigen und die Zündung
einschalten, bedeutet das nichts anderes als das Aktivieren der Zündspule. Der Dreh am
Zündschlüssel schaltet die Batteriespannung von zwölf Volt auf den Niederspannungsanschluß der
Spule. Beim Starten schießen dann bis zu 30 000 Volt aus ihrem Hochspannungsanschluß, die einen
kräftigen Zündfunken erzeugen. Das Geheimnis dahinter nennt sich elektromagnetische Induktion. Denn
die Zündspule besteht in Wahrheit aus zwei ineinander verschachtelten Spulen, der Primär- und der
Sekundärspule. Wenn eine Spule, also ein aufgewikkelter Kupferdraht, von Strom durchflossen wird,
entsteht in ihrem Umkreis ein Magnetfeld. Die zwölf Volt fließen in die Primärspule, die die
Sekundärspule umgibt. Damit liegt diese komplett im Magnetfeld. Im Vergleich zur Primärspule
besitzt sie 50- bis 150mal so viele Windungen, außerdem ist ihr Draht wesentlich dünner. Zusätzlich
besitzt sie in ihrem Zentrum einen Eisenkern, der das Magnetfeld weiter verstärkt. Er besteht aus
zahlreichen dünnen, gestanzten Blechscheiben, so wird das Magnetfeld besser verstärkt als mit einem
großen Eisenklotz. Allerdings wurde bis jetzt noch kein Zündfunke ausgelöst. Das passiert auf ganz
einfache Weise: Der Strom in der Primärspule wird abgeschaltet. Im selben Bruchteil einer Sekunde
bricht ihr Magnetfeld zusammen, und das Phänomen der elektromagnetischen Induktion tritt auf: In
der Sekundärspule entsteht eine Spannung von einigen Tausend Volt. Nur für einen kurzen Moment,
aber lang genug, um einen Zündfunken auszulösen. Früher genügten etwa 15 000 Volt, um eine
zuverlässige Zündung auszulösen. Heute werden für Turbooder Kompressormotoren und
Benzindirekteinspritzer rund 30000 Volt benötigt. Womit aber noch nicht geklärt ist, wann der Funke
ausgelöst wird. Heute entscheidet darüber die Elektronik, sie errechnet sogar für jeden Zylinder
einzeln den richtigen Zündzeitpunkt. Bis Anfang der 80er Jahre gab es dafür einen Kontakt, der vom
Motor angetrieben den Primärstrom im richtigen Moment unterbrechen mußte - den Unterbrecherkontakt.
Seine Verschleiß- und Einstellungsempfindlichkeit führte dann zu einem berührungslosen Auslöser,
der bis Ende der Neunziger die Zündspule steuerte. Allerdings ist es mit der Auslösung der
Zündspannung allein nicht getan, sie muß auch zum richtigen Zylinder geführt werden. Wie das
funktioniert, lesen Sie weiter.
Der Zündverteiler
Woher weiß eigentlich der
Zündfunke, welcher Zylinder zünden soll? Das bestimmt der Verteiler, er ist die Weiche, die den
Funken auf den richtigen Weg führt. Wie aus den vorigen Folgen bekannt ist, benötigt der
Viertaktmotor pro Zylinder alle zwei Umdrehungen einen Zündfunken. Deshalb wird der Verteiler mit
eben der halben Kurbelwellendrehzahl angetrieben. Wie die Nockenwelle - weshalb die oft den
Verteiler in Gang setzt. Herzstück des Verteilers ist die Verteilerkappe, in ihrer Mitte befindet
sich der Anschluß für die Hochspannungsleitung der Zündspule. Außenherum angeordnet die Anschlüsse
für die Zündkabel, die zu den einzelnen Zylindern führen. Maximal sind es acht, bei entsprechend
großem Durchmesser der Verteilerkappe. Bei früheren Zwölfzylindern hingegen wurden stets zwei
Verteiler für je sechs Zylinder benutzt. Innerhalb der Verteilerkappe rotiert der Verteilerfinger
oder auch -läufer. Er ist so mit der Kurbelwelle des Motors synchronisiert, daß er mit seiner Nase
stets auf den Anschluß zeigt, der mit der nächsten Zündung an der Reihe ist. Daher müssen die
Zündkabel auf der Kappe in einer Reihenfolge eingesteckt sein, die der Zündfolge des Motors
entspricht. Bei einem Reihenvierzylinder führen die Kabel also der Reihe nach zu Zylinder eins,
drei, vier und zwei. Damit sind die Aufgaben des Verteilers aber noch nicht vollständig
umschrieben, schließlich heißt er mit vollem Namen auch Zündverteiler. Denn die Techniker kamen
schon recht früh auf die Idee, in seinem Untergeschoß den Auslöser des Zündfunkens einzubauen
(siehe Folge zwölf: Zündspule). Dieser Ein-/Aus-Schalter bestand bis vor rund 20 Jahren aus einem
Kontakt, der von Nocken auf der Verteilerwelle - pro Zylinder einer - gesteuert wurde. Und weil der
Zeitpunkt der Zündung bei unterschiedlichen Fahrbedingungen zu verschiedenen Zeitpunkten erfolgen
sollte, wanderten die Verstelleinrichtungen dafür - Unterdruckdosen und Fliehkraftversteller -
gleich mit in den Verteiler. Der mechanische Zündkontakt wurde ab den achtziger Jahren zwar durch
ein elektronisches System ersetzt. Dabei rotiert ein Blenden- -rad mit Ausschnitten über einem
Sensor. Kommt ein Ausschnitt, wird gezündet. Trotzdem blieb der mechanische Verteiler ein
anfälliges System. Deshalb begannen sich vor etwa 15 Jahren die rein elektronischen Zündungen
durchzusetzen. Heute besitzt jede Kerze ihre eigene Zündspule, die Elektronik berechnet den
Zündzeitpunkt für jeden Zylinder bei jeder Umdrehung neu.
Das Dieselprinzip
Wenn Techniker vom Selbstzünder reden, meinen sie den Dieselmotor. Denn der kann, anders als
der Benziner, auf eine Zündanlage verzichten. Das ist nur möglich, weil er sich eines
physikalischen Phänomens bedient: Wenn Luft zusammengedrückt - also komprimiert - wird, erwärmt sie
sich. Je stärker der Druck, desto höher die Temperatur. Wird sie beispielsweise von etwa einem Bar
(dem normalem Außenluftdruck) auf 30 Bar komprimiert, erreicht sie dabei eine Temperatur von
ungefähr 700 Grad. Ein Tropfen Kraftstoff, dort hineingespritzt, verbrennt sofort. Beim Diesel
übernimmt der Kolben, wie auch beim Otto- Viertaktmotor, diese Verdichtungsarbeit. Der erste Takt
sieht ebenfalls ähnlich aus: Das Einlaßventil öffnet, nur strömt beim Diesel statt eines
Kraftstoff-Luft-Gemisches reine Luft in den Zylinder. Und weil heutzutage fast alle Diesel einen
Turbolader besitzen, muß der Kolben diese Luft beim Abwärtsgehen nicht mühsam ansaugen, sondern
bekommt sie unter Druck verabreicht. Der wieder aufwärts eilende Kolben komprimiert nun bei
geschlossenen Ventilen diese Luft, bis sie nur noch rund ein Zwanzigstel ihres Volumens einnimmt.
Je nach Motortemperatur und Ladedruck des Turbos beträgt der Druck im Brennraum nun zwischen 30 und
100 Bar, die Temperatur der Luft 700 bis 900 Grad. Dort hinein wird jetzt der Dieselkraftstoff
eingespritzt. Knapp bevor der Kolben seinen oberen Totpunkt erreicht. Denn es dauert den Bruchteil
einer Sekunde, bis die Verbrennung beginnt - der sogenannte Zündverzug. Dann aber verbrennt der
Kraftstoff schlagartig, die Abgase dehnen sich aus, die Temperatur im Brennraum steigt noch weiter
an und insgesamt auch der Druck. Bei Vollgas drücken nun bis zu 200 Bar auf den Kolben, stemmen ihn
abwärts und setzen so die Kurbelwelle in Umdrehung. Grundsätzlich entwickelt ein Diesel um so mehr
Kraft, je höher die Menge des eingespritzten Kraftstoffs ist. Allerdings muß der Sprit auch
genügend Luft und damit Sauerstoff für die Verbrennung vorfinden. Denn unverbranntes Dieselöl
erzeugt Ruß, der entweder als Qualm aus dem Auspuff quillt oder aufwendig gefiltert werden muß.
Deshalb muß der eher zähflüssige Dieselkraftstoff mit hohem Druck eingespritzt werden, damit er von
den winzigen Löchern in den Einspritz-düsen möglichst fein zerstäubt wird. Denn nur so findet jedes
Kraftstoff-Teilchen auch einen Sauerstoff-Partner zum gemeinsamen Verbrennen. Wie das funktioniert,
lesen Sie nächste Woche.
Die Diesel-Einspritzung
Der Diesel führte
lange Jahre ein beschauliches Leben: Die Leistung war Nebensache, Schadstoffe erst recht. Und so
drückten die Einspritzdüsen den Kraftstoff mit maximal 120 bis 140 Bar Druck in die Brennräume. Das
änderte sich Anfang der 90er Jahre mit Einführung der Direkteinspritzer schlagartig. Diese Technik
benötigte Einspritzdrücke um 800 bis 900 Bar, um reichlich Leistung und wenig Qualm zu erzeugen.
Dafür wurden Verteiler- Einspritzpumpen benutzt, die - wie der Zündverteiler mit dem Funken - den
Kraftstoff entsprechend der Zündfolge in die Zylinder einspritzen. Das funktionierte weitgehend
mechanisch mit nur wenigen elektronischen Stellelementen. Doch steigende Anforderungen an Leistung
und Umweltfreundlichkeit führten zur Entwicklung eines Systems, bei dem sich Einspritzzeitpunkt und
-menge völlig frei von mechanischen Zwängen programmieren lassen - die Common-Rail-Einspritzung.
Common Rail bedeutet gemeinsame Leitung. Die verbindet die vom Motor angetriebene Hochdruckpumpe
mit den Einspritzdüsen aller Zylinder und besteht aus hochfestem Stahl. Denn sie muß heute bereits
Drücke bis zu 1600 Bar aushalten. Selbst die erste Generation von 1997 spritzte schon mit 1350 Bar
ein. Das Signal für die Einspritzung gibt die Elektronik, die Daten zu Menge und Zeitpunkt werden
für jeden Zylinder jedes Mal neu berechnet. Dafür bedient sich die Elektronik zahlloser Sensoren.
Unten sind nur die wichtigsten gezeigt. Denn die Elektronik weiß auch jederzeit über die genaue
Stellung der Kurbelwelle Bescheid, kann so pro Arbeitstakt für jeden Zylinder mehrere
Einspritzvorgänge auslösen. Die Voreinspritzung (oder auch Piloteinspritzung genannt) dient dabei
dem Anwärmen des Brennraums, verringert so das Geräusch der Hauptverbrennung. Und gezielte
Nacheinspritzungen zu deren Ende heizen den Katalysator an oder helfen einem Rußfilter beim
Freibrennen. Common Rail ist bei allen neuen Dieseln Standard. Und bald auch im VW-Konzern, der
seit Ende 1998 bei seinen Drei- und Vierzylindern auf das eigene Pumpe-Düse- System gesetzt hatte.
Damit ist Volkswagen bis heute Druck-Rekordhalter: 2050 Bar. Aber der Aufwand ist enorm. Nicht nur,
daß jeder Zylinder eine eigene Pumpe bekommt - auch deren Antrieb über die Nockenwelle muß
entsprechend kräftig ausgelegt sein. Was Pumpe- Düse erheblich teurer macht als die
Common-Rail-Einspritzung.
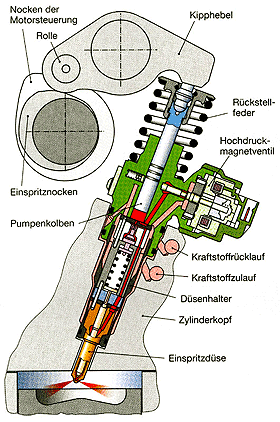